Vibration Data Meets Process Control Data
We are thrilled to partner with OSIsoft, a global leader in operational intelligence, to bring the merits of vibration data and process control data to the industrial world. Arun Santhebennur, Cofounder of Petasense, recently authored an article which first appeared on OSIsoft’s website. Read the complete blog post here:
The Digital Wave
Industrial IoT or Industry 4.0 presents a great opportunity for manufacturing companies to improve their bottom line. A big priority for most Fortune 1000 industrial companies today is digitization. But what does it exactly mean to go digital and how does a company go about making it happen? According to McKinsey’s report Unlocking the Potential of the Internet of Things, Predictive Maintenance (PdM) is the biggest use case for IoT technology and digitization in manufacturing. It is expected to have a potential economic impact of up to $3.7 trillion a year by 2025.
Most plants that were set up in the last few decades use a run-to-failure or time-based maintenance model for the upkeep of their equipment. As facilities embark on their digital transformation journeys, one of the biggest hurdles they face is that their critical machinery is just not instrumented. In other words, most equipment used in the factory does not come preinstalled with sensors (vibration, current, ultrasound, etc.) that monitor asset health. The fact that most data analysis in the industrial world today is manual presents an additional problem.
Industrial IoT is solving these challenges by democratizing predictive maintenance, making it easy and affordable. Technology trends like wireless connectivity and miniaturized low-cost MEMS sensors are making the instrumentation process a lot faster, simpler, and more affordable. Cloud infrastructure and machine learning are making data analysis automated and scalable.
While the GEs and the IBMs are realizing the importance of capturing all that machine data and are now building cloud platforms, OSIsoft has been in the business of building data infrastructure for 35+ years with 1.5B+ licensed sensor-based data streams.
“The first step in IIoT for many industrial companies and utilities is capturing data from their legacy equipment. Many of these systems – while they work fine – are years, if not decades, old and weren’t created with digital in mind,” said Pat Kennedy, CEO of OSIsoft. “Our partnership with Petasense will help lay the foundation for digital transformation.”
Petasense and OSIsoft
Petasense is a easy-to-deploy, end-to-end predictive maintenance solution for monitoring the health of critical rotating machines like motors, pumps, and compressors. The Petasense solution consists of a patent-pending wireless vibration sensor, cloud software and machine learning analytics. It is trusted by industry leaders to improve uptime, asset reliability, productivity, and reduce unnecessary repair costs.
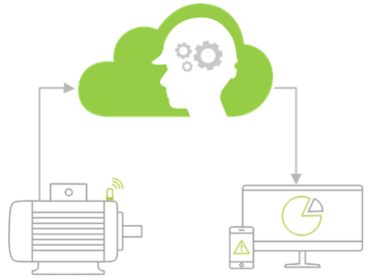
By analyzing vibration characteristics, Petasense machine learning software is able to flag anomalous vibration and predict common defects like pump cavitation, bearing wear and misalignment. These ML algorithms compute a proprietary numerical machine health score that facilitates plant managers to make real-time, data-driven maintenance decisions.
OSIsoft is a global leader in operational intelligence. OSIsoft’s PI System is an enterprise-wide data infrastructure for collecting and monitoring operational data. The PI System captures data from sensors, manufacturing equipment and other devices and transforms it into rich, real-time, actionable insights. It enables industrial customers to manage assets, mitigate risks, comply with regulations, improve processes and drive innovation.
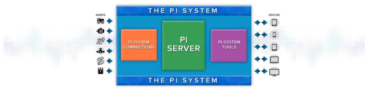
Process and Reliability Data Lived In Two Separate Worlds
Picture how a natural-gas-fueled power plant would typically monitor the health of a critical water injection pump or a boiler feed pump. Traditionally, the power plant would continuously monitor process variables such as pressure, flow or temperature of the plant water. The process information would then be collected in the DCS system and trended in the PI System.
However, the reliability data (such as vibration or current draw of a pump) would be collected a few times a year through manual walk-around programs, using handheld data collectors. Reliability data would then be siloed from operational data. Similarly, the data surrounding building energy management would often be captured by another system. While these data sources can easily be combined in the PI System, customers often don’t think about unifying them, making it more difficult to see the big picture. Failure to break these data silos could mean that a critical bearing failure goes undetected, resulting in unplanned downtime and unanticipated repair costs.
The OSIsoft and Petasense Partnership Is Revolutionizing Predictive Maintenance
Petasense and OSIsoft are joining hands to pave the way for integration of process control data and vibration data. This partnership will enable industrial customers to retrofit their machinery with wireless sensors and perform predictive maintenance by correlating process and vibration data. This will help plants eliminate unplanned downtime, improve plant safety and reduce repair and maintenance costs. The control center staff will be able to get real-time alerts when vibration levels on critical rotating machines exceed alarm limits directly in their PI System.
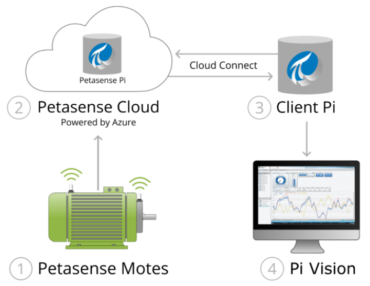
The Case of Silicon Valley Power
Silicon Valley Power (SVP), the municipal electric utility owned by the City of Santa Clara, has signed on to integrate OSIsoft and Petasense solutions. Today, SVP monitors all its balance-of-plant (BOP) rotating machines with Petasense.
“After a successful trial, we have now rolled out the Petasense solution to cover all our mission critical rotating machinery,” said Paul Manchester, Assistant Plant Manager at SVP, adding that “we are now integrating Petasense and the PI System to capture additional value and realize greater operational efficiencies.”
The integration of the two systems will enable SVP to correlate asset and process data and create predictive models that leverage vibration along with other process parameters. Going forward, SVP is planning to maximize asset reliability and process performance because their engineers will be equipped with a multi-parametric view of the data, better insights and more powerful analytics to make informed maintenance decisions.
Conclusion
Industry 4.0 has enabled the collection of maintenance and process data at scale. With IoT it is now possible to retrofit machinery with sensors and collect maintenance data at a size and scale that was unimaginable before. Any site that uses PI System will be able to easily deploy and implement predictive maintenance at an extremely affordable price point.