Any real sense of reliability training returning the greatest possible value must be based upon the needs of the business and the future growth and technology, extending to every individual and department. Reliability training must not be conceived as something to improve the skills of the lowest technician but to improve the skills of every technician.
Reliability training, to be of the greatest value to any organization, must be planned and schedule the same as any other job or task and directed toward a definite goal. The place to start any reliability program is at the top of the organization. If the leader or manager in charge of the business unit does not believe that he needs a reliability program or training and is not willing to make the effort to get it or step out of there box, then there is little possibility that as a leader or manager they will be able to inspire their team with the need for reliability.
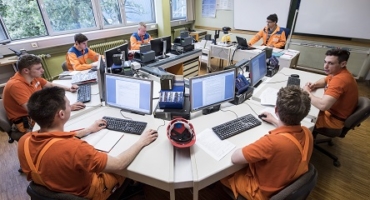
It is found to be an almost universal rule unless the reliability leader or manager are studying and growing and have been able to inspire their team with the enthusiasm for learning and demonstrating reliability practices then the reliability program and training will be perfunctory matter, poorly conducted and depending upon the enthusiasm of a few technicians to keep it alive and eventually will be thrown overboard.
The reliability leader/manager and technician who considered that their education and training are finished when they took on the responsibilities or position will fail soon. The recognition for the need of continuous growth is one of the signs that this is has become a profession and skill. Successful reliability leaders and technicians are realizing that a large body of information, based on research, data and experience, and training in a multitude of disciplines in reliability will embody the successful solution to countless problems in maintenance. It is probable that at the present moment this body of knowledge in reliability is growing faster than any corresponding body in any of the other profession. New technology is springing up in a remarkable manner in every discipline of reliability. The reliability Industry is changing at every point that no one individual can hope to keep track of the developments.
A coach, mentor, and teacher in the reliability profession is the reward of winning a race. Nowhere is the race sharper, the rewards greater, and decreasing asset failures more frequent, and with the new technology so essential to victory so numerous, one must always be seeking out education, training and conferences for best practices in reliability.
Reliability training that makes full use of all opportunities inside and outside of the organization, that is engaged in the introduction of reliability training and best practices to new technician and older technician in the understand and teaching of better methods; and in the coordination of reading, lectures, conference and training, will bring that maintenance organization to world-class performance.
In my 35 years in maintenance and engineering continual training and education in maintenance and reliability, best practices have always been an ongoing project for me, it has never stop! I am always seeking out new ideas, new technology, and information to help me grow and to also help my team grow.
In teaching on the college level for Industrial maintenance, I have taught reliability and precision maintenance to the up and coming maintenance technicians, to give them a solid base of understanding on reliability and precision maintenance, so when they graduated, they had a basic understanding of what reliability maintenance and best practices are.
As a reliability leader or reliability technician, you can wake up every day and curse the darkness or you can light the way through your action, you have a choice but the right choice is taking the time to learn and doing it correctly the first time.
We need reliability/maintenance leaders and technicians who know and understand the Reliability Body of Knowledge Elements and who are willing to step out of there box and teach either thru training, education, and conference on reliability/precision maintenance to their teams, when this is done it will make their teams stronger and will align maintenance with corporate business goals.