About the Author
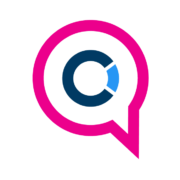
Working around electrical equipment, it’s imperative to understand the potential hazard of arc flashes, what causes them, and how to prevent serious damage to people and assets. When electrical current passes through the air from one point to another, the resulting arc flash can reach temperatures up to 35,000° F. An arc flash is the light, concussive energy, and heat produced as part of an arc fault, a type of electrical discharge that results from a connection from phase to phase, or phase to ground. It can also occur (or jump) from air to ground, as in medium to high voltage.
An arc flash can be due to poor maintenance, failing components, design flaws, and low resistance that allows voltage to follow a path that is hazardous and potentially explosive. We can mitigate some conditions, from destructive corona in high voltages to over stuffing conductors in a conduit, by implementing good practices and adhering to NEC codes. But the single greatest cause of arc flash, human error or complacency, is another matter. It’s easy to forget the explosive nature of electricity, thinking it’s only 480v, when in fact it’s just 240v. And then there’s the case of electricity following an unintended path, in which case, an arc flash will occur every time.
The following are some underlying, preventable causes:
It’s the degree of outcome that causes damage. The three components of an arc flash have varying degrees of damage:
An arc flash hazard assessment is a workplace evaluation to identify arc flash dangers, and to determine their likelihood of causing injury or death. Arc flash hazards are clearly defined by the National Fire Protection Association (NFPA) standard 70E, which is recognized by OSHA and must be followed under various OSHA regulations.
The hazards identified in the assessment are categorized and a comprehensive plan developed for how to mitigate the effects of such a hazard. The “levels” of PPE required are formulated, based on the nature and degree of the hazards for the functions being performed at various distances from the hazard.
OSHA code 29 CFR 1910.333 (a) is the regulation that speaks to arc flash. The National Fire Protection Association (NFPA) has published the standards in NFPA70E: Standard for Electrical Safety in the Workplace. While not a mandatory regulation, it is one that you will be cited for if a recordable event occurs. Also, when calculating the risk, IEEE 1584 is the method used most often.
Qualifications for performing engineering studies, like an arc flash assessment, varies from state to state. Best practice is to have a firm with a licensed Engineer on staff who oversees the assessment reports, at a minimum. Data gathering and calculations are standardized in a straightforward manner by IEEE 1584, as well as NFPA70E. Most assessments are completed via an automated program that performs all the calculations, in accordance with the recognized specifications of the governing bodies.
OSHA can issue a citation for not addressing arc flash, as it is a known hazard. They can issue (and have issued) citations under the General Duty Clause and can reference the NFPA 70E within this citation. It stipulates that workers shall be provided with PPE, tools, and test instruments to minimize risk, but first they must be warned of the risk through an arc flash warning label. Like most rules (or suggestions), compliance can be “negotiated” unless something happens. While OSHA is good at investigating and fining for deficiencies, it does not do tons of proactive screenings and what it does do is voluntary.
The easiest way to minimize the risk is the assessment. After doing the research and rating the potential risks, a label of the required PPE and the hazards is placed on each panel of equipment. This will help mitigate the impact of an arc flash. As for preventing one, it takes sound documented procedures and a hierarchy of who can open live equipment. The only way to truly avoid arc flash is de-energize (shut down) equipment prior to opening it.
Any piece of equipment included in an arc flash assessment must have a label describing many different values and levels of PPE. Most important is when the assessment was done and by whom. These labels must be in a clearly visible position that can be easily read. They also must be durable and not fade or fall off. This label is the first line of defense for anyone who may need to open the equipment.
A qualified worker is one who is trained in the craft for the equipment. Additionally, they have been through arc flash training and understand the terms and conditions spelled out for “hot” work. And finally, they can demonstrate work practices that are safe and follow established procedures. The biggest risk of failure for any company is allowing untrained or unqualified personnel to perform work on live circuits.
In the food and beverage manufacturing process, heavy use of liquids or water make arc flash, or electrocution, much more of an issue. Most liquids offer an easy path to danger for electrical current. Also, most of the incidental injuries occur when the service person is trying to rush and clear a problem. As mentioned earlier, most electrical accidents are a result of human error or carelessness. The liability is on the business, not the individual, so a hazard assessment helps protect all parties.
Arc flashes can cause severe damage and injury. Such occurrences are avoidable, to some extent, by providing proper training and performing an arc flash hazard assessment of all electric equipment. These assessments should be done by a qualified person and in accordance with industry standards and regulations. Follow-up labeling of equipment is another critical component to ensure the effectiveness of this safety procedure.