About the Author
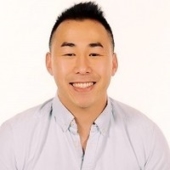
Maintenance and reliability managers must have metrics in place to identify needs for improvement. Metrics are also extremely important for validating whether the maintenance team is headed in the right direction to achieve the organization’s goals and objectives. There are dozens of reliability metrics, but not every measurement applies to every organization.
Which maintenance metrics are important to your company depends on your industry, the types of assets, and your company and departmental goals and objectives. Instead of juggling with countless measurements, it is a good idea to choose a few KPIs that you think are important and suitable for your organization and department.
Here’s how you can measure and use some essential maintenance Key Performance Indicators (KPIs) that apply to most companies:
MTTR, also referred to as maintainability measures the ability to do maintenance to keep or restore equipment to a specified operating condition. Using MTTR, you can find the average time it takes your maintenance staff to reinstate a machine to its optimal working condition following a breakdown.
You can use the findings to expedite the machine’s restoration time, which can help decrease losses resulting from downtime.
MTBF forecasts the time between one failure to the next under normal operating conditions. In other words, this KPI helps you predict the life expectancy for a piece of equipment.
If MTBF for specific equipment comes out higher, it indicates that the machine will work longer before eventually breaking down.
MTBF gives you an idea as to how long the equipment will work without failure, so you can easily plan for preventive maintenance or replacement.
Availability
Availability, also known as uptime, calculates how likely it is for a piece of equipment to operate decently well under reasonable conditions. It is an essential metric for measuring the overall effectiveness of an asset.
A tangible asset loses its availability as it is used over time. Technicians can improve the asset’s availability by undertaking essential maintenance tasks. And when availability drops below a specific threshold, the asset’s performance will not improve unless it is upgraded or replaced.
Using this KPI, you can identify opportunities for improvements, in addition to reducing the risk of sudden equipment failure.
The typical availability benchmark is 95 percent for most assets. However, it can differ depending on how necessary the equipment is to your operations.
PPC denotes the percentage of time spent on planned maintenance in contrast to unplanned maintenance tasks. In other words, it tells you how much time your technicians spent on preventive maintenance as compared to time spent to fix unexpected failures.
Ideally, at least 90 percent of planned maintenance time is necessary for optimal productivity.
You can use the findings of PPC to strengthen planned maintenance and reduce the likelihood of unexpected failures.
OEE measures the effectiveness of your company’s maintenance program, depending on the quality, performance, and availability of a piece of equipment.
If OEE comes out 100 percent, it shows that your asset is operating at optimum productivity level, without presenting any signs of defects.
Using this KPI, you can gain insights into how an asset is performing and decide if there is room for improvement. It helps you identify defective assets that are affecting your productivity in negative ways, so you can eliminate the flaws or replace the assets.
OEE Any Def. of Quality in the last calculation?