Who does cost avoidance? What is it? Where would you apply it? Why would you worry about it? These are the questions that one should ask themselves. In the world of Predictive Maintenance, we are busy gathering samples, taking vibration readings, analyzing trend charts, inspecting electrical components, reporting the finds back to the process owners and following up on Work Orders issued. Most of the time is spent doing the physical work and analyzing that data to determine the condition or health of the equipment rather than thinking what our group did to save the company money. This article explains the methodology we used and why you should care about cost avoidance.
Our Plant Operating Team asked our group a question of how effective we were at our jobs. We did have some metrics that we track that answered that question. As the discussion evolved, it boiled down to money. In the work that we do, what is the total amount of money that we saved the company? Another way to look at it is what level of spending did the plant avoid because the PdM department was here in
house? We thought long and hard about this and worked through a methodology to use with each program so we could successfully track cost avoidance year after year.
The programs that our PdM department employs are as follows:
- Vibration Analysis
- Oil Analysis
- Oil Usage
- Thermography
- Ultrasound
- Exhaust Ventilation
For each of the listed programs we had to systematically come up with a method in which to capture the costs for the following question. “If the PdM department wasn’t here, what would the company do?” Thinking about it in the sense that if we weren’t here at all, gave us a better vision of what the costs would be to resolve issues that arose. It may be a vibration analyst would be called in to do a comprehensive study on the equipment’s health. It could be trades would replace a motor when that wasn’t the problem in the first place. Engineering may have to call in contractors to provide them with a thermal scan on a machine that’s intermittently shutting down. In this article, we will discuss Thermography and how we derived at the costs.
We started by listing the most common types of infrared finds that we have had: fuses, main disconnects, etc. Within each of these groups we were then able to list specific parts within that group: wire, connections, clip, block, etc. Next, we had to enlist the help of Electrical Trades that would be able to assist us in putting an estimated time to repair for each of the line items listed. Along with that came a lot of research on how much the electrical parts cost to which we spent time questioning our in-house Stores team along with other electrical suppliers. Below you can find an example of some of this work.
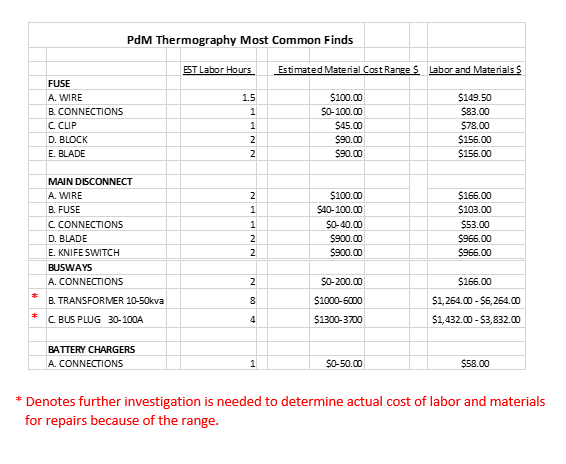
We modeled the thermography cost avoidance to follow a downtime failure analysis 6 Sigma (6S) project that I completed for our vibration program. This project identified three categories of severity: Simple, Compounded and Complex. We found that by associating each category with the delta temperature of the thermal finds we could conservatively arrive at a total estimated cost for each type of specific find we had. One thing that we could not factor in easily was the fire related damage and personal injury costs if something failed. When something fails, there typically is secondary damage that occurs because of the failure. The costs we came up with in the “Most Common Finds” list only applies to the component itself along with repair labor. Then, as discussed earlier, each specific find is put into a severity category: simple, compounded, or complex. These categories along with the delta temps are listed below for the different equipment that we monitor.
For finds on electrical cabinets:
- Simple Category = (no work order issued for this category)
- Compounded Category = 20F – 49.9F
- Complex Category = over 50F
For finds on busways:
- Simple Category = 1F – 5.9F
- Compounded Category = 6F – 11F
- Complex Category = over 11.1F
For finds on MCCs:
- Simple Category = 5F – 19.9F
- Compounded Category = 20F – 50F
- Complex Category = over 50F
Each one of these categories carry different assumptions based off our 6S vibration downtime failure analysis project. These assumptions include an estimate of the downtime that would occur, costs for Direct labor, Trade’s labor, Engineering labor, Support labor, any outside contractor labor if applicable, and any other materials needed for the repairs. We keep a rolling list throughout the year on all infrared finds and the repairs made. We can calculate the total cost avoidance by associating the find to one of the severity categories. This total cost avoidance is what we communicate to the Plant Operating Team each year.
The example below shows a loose connection that has occurred on a busway that provides power to office areas. The delta of this find is 9.9F. The labor and material costs associated with this find was $166 as was listed on our Most Common Finds list for busway connections. The total cost avoidance calculated due to a failure is $2284, the cost for the compounded category for busways.
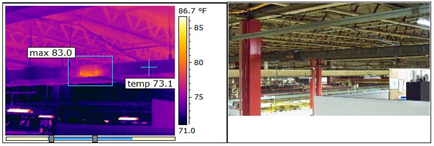
The next example is a loose wire connection on a bearing grinder on the Camline. The delta is 40.3F. For this issue, we assigned $58 for the cost avoidance to be listed on the work order. The total cost avoidance would be $2284, the cost for a compounded category for electrical cabinets.
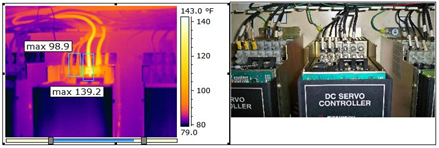
The next example is a fuse connection on a main disconnect that controls the natural gas compressor for the Engine Test team. The delta is 74.9F. We assigned $78 for the cost avoidance, however the total cost avoidance for this find was $6312 due to the delta being greater than 50F. This example would fit into the Complex category for electrical cabinets. We issued a Safety work order for this find because the delta temperature was >50F. This allows the Trades to prioritize their work to correct this issue immediately.
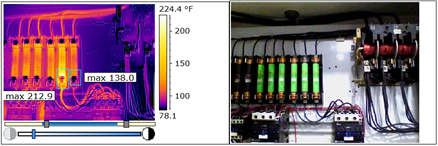
On top of the electrical cabinet inspections that we perform, our PdM department has also taken on the annual roof scan, the semi-annual MCC scans and the busway scans. In the years past, our company contracted that work out. Through some research and by working for several years with this infrared contractor, we learned how to perform the thermal roof scans and what conditions were needed to perform a good thermal roof scan. We now fully perform the yearly scan and avoid paying the money for the need to contract this service out; the same applies for the MCC and busway scans. With our PdM group performing these previously contracted services we can save the company a total of $10,000 annually. On top of that, we haven’t even discussed the energy savings that are created by fixing these finds. After discussing this with our Plant Engineering group, we calculated that by identifying and repairing the infrared finds we can save $15,000 annually in energy savings!
The graph below includes all PdM programs and the cost avoidance associated with each of them by year.
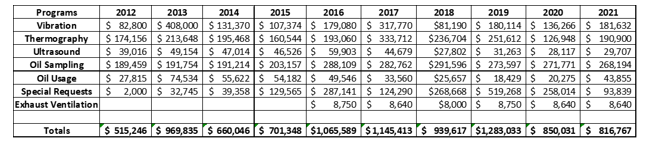
When management is asking you to justify your job, what will you say? We can safely say that through the programs that we utilize in our three person Predictive Maintenance group, the Jamestown Engine Plant has avoided paying more than triple our salaries since we started tracking cost avoidance.
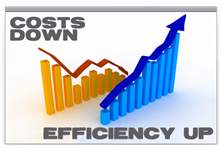