About the Author
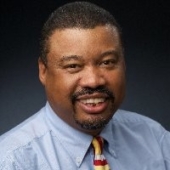
Ray Dalley has been performing research, manufacturing, sales and marketing with ferrography (wear particle analysis) for the
past 30 years.
Ferrography has been around since the 1970’s invented by Vernon Westcott due to a need to observe wear particles/Ferrography in the 5–350-micron range. Most believe this is the particle size range to detect potential failure prior to any mechanical problems. However, the ferrography analysis was thought to be time consuming, expensive, and non-repeatable.
My presentation will discuss the work involved with NASA Space James Webb Telescope application, the heat-treating process in ferrography, heat treatment of glass patch and the advancement of image analysis with wear particles.
With the development of computers and the ability to store, quantify, and highlight pattern behavior on video images the ferrography technology has risen to new heights to detect problems on mechanical moving parts such as Gearboxes, Compressors, Gas Turbines and Diesel Engines. In addition, ferrography can analyze Greases, Hydraulic Fluid and Aqueous Solutions. Outlining these attributes allows Ferrography to investigate many applications without limitations potentially using AI. And now, Ferrography has a new Neodymium Magnet design which increased the capture capability of Wear Debris.
The original magnet design was over 10 pounds heavy and measured 3 Inches by 10 Inches by 2 Inches tall. The new Magnet design is lightweight and very small in comparison weighing 6 Ounces and measuring 1 Inch by 4 Inches by ½ Inch tall. This dramatic design change enables the future of this technology to be reduced to a portable instrument or an On-line device keeping the future bright.
Analytical Ferrography utilizes a glass substrate that is prepared by using a Ferrogram Maker. The Ferrogram Maker deposits 3ml of an oil sample on the glass substrate at a calculated rate, passing across a high magnetic field. Wear particles arrange themselves along the slide with the largest particles being deposited first.
Ferrous particles line up in strings that follow the magnetic field lines of the Ferrogram Maker. Nonferrous particles and contaminants travel down in a random distribution pattern not oriented by the magnetic field. The glass substrate is then run through a rinse cycle which allows the particles to be tightly adhered to the substrate called a Ferrogram. The Ferrogram is now ready for Ferrographic examination with a Bichromatic Microscope.
Ferrous from nonferrous can easily be distinguished due to the alignment with the magnetic field in ferrography. However, trying to identify what type of steel or bearing material becomes very difficult unless you practice using the Heat Treatment method for final examination in Analytical Ferrography. This is where Heat Treating the ferrogram is necessary. The Heat Treatment process is simple, and the instructions are as follows:
Position the surface thermometer on the hot plate. Turn on the hot plate to approximately one third its maximum value. Let it settle at its current temperature for fifteen minutes before any further adjustments are made. Once the hot plate has reached a constant temperature, adjust the temperature control dial until the thermometer shows a steady temperature of 330oC or 625oF. Mark the dial to indicate where the dial needs to be for this temperature.
Ferrograms are typically examined under a microscope that combines the features of a biological and metallurgical microscope. Such equipment utilizes both reflected and transmitted light sources, which may be used simultaneously. Green, red, and polarized filters are also used to distinguish the size, composition, shape, and texture of both metallic and non-metallic particles. The diagnostic capabilities of the technology step forward until it is time to identify the metal composition.
Once wear particles are observed the Analyst can determine the type of particle (gear and bearing wear, abrasive/cutting wear, sliding wear, etc.) and measurements can be made to determine the size of these particles. With Analytical Ferrography one of the final steps in the analysis is to place the glass substrate on a hot plate, typically at 330°C. This is done for approximately 90 seconds. The observed particles will form temper colors upon heating, thus allowing the Analyst to determine the composition of the wear particles. Various Ferrous and Nonferrous materials, such as Low Alloy Steel, Case Hardened Steel, and Babbitt, can then be identified by changing temper colors.
Temper colors is due to the growth of a thick oxide layer on metal when it is heated in air. For ferrous alloys, the growth rate is restricted by alloying elements. Steel, which has relatively few alloying elements, has the quickest oxide layer growth rate. Cast iron, which typically has much higher carbon content, has a slower oxide layer growth rate. High alloy steels, which are made with significant percentages of nickel, chrome, and other elements, are most resistant to the growth of oxide layer. The temper color phenomenon most utilized is the first stage of heat treating at 330 Celsius for 90 seconds on the hot plate which allows distinction of ferrous particles into three broad classes: low alloy steel turns blue, medium alloy steel (Cast Iron) turns straw, and high alloy steel stays unaffected.
This is vitally important to NASA operating the largest clean room in North America located near Washington DC. The cleanroom has over 20 compressors in case of any failure occurring they have a number of redundant backups not to lose any time polishing the mirrors for the telescope. The chiller system is driven by Lufkin speed increaser gear box driven by a Westinghouse 2500 horsepower induction motor. The bearings at the free and driven end of the motor are sleeve bearings along with labyrinth seals. The drive end holds 1.6 gallons in the sump and the free end holds 1.1 gallons of oil.
Testing of the oils is on a scheduled basis monitoring the condition of the motors, bearings, and the gearbox.
These mirrors are quite large and very expensive, costing over several million dollars each. Example the James Webb Space Telescope cost was over $8 billion US Dollars. Prior to take off last year. Therefore, quality, reliability and predictive maintenance were very important and necessary.
The NASA James Webb Case Study shows an increase in both Sand, Dirt, Sliding Copper Wear and Bearing Wear particles recommending an oil change and maintenance action to determine the origination of the wear debris. Feedback from NASA indicated the oil being purchased needed inspection and filtering prior to filling the driven ends of the motor shaft, gearbox and compressor. Another case of using ferrography correctly to pinpoint the issues for a high price machinery.
Filter Patch Testing
Filter Patch Testing is an effective tool in detecting wear particles in lubricants, especially in equipment that utilizes babbitted bearings. Filter Patch Testing is a method by which a specified volume of fluid, typically 25ml, is filtered through a membrane filter of known pore structure. All particulate matter more than an “average size,” determined by the membrane characteristics, is retained on its surface. Thus, the membrane is discolored by an amount proportional to the particulate level of the fluid sample. The patch is then analyzed with either a Stereo Microscope or a Bichromatic Microscope. When there is an abundance of visible particles on the patch, sometimes a magnet is repeatedly moved under the patch to possibly determine if the particles are Ferrous or Nonferrous.
In the past this heat treatment procedure could not be accomplished with a typical filter patch due to the cellulose nature of the material. If the patch were placed on a hot plate at the suggested temperature, it would virtually burn away and could no longer be utilized for analysis. This limitation not only left the Analyst without knowing the composition of the particles, but also whether the particles are of a Ferrous or Nonferrous nature.
Numerous studies in attempting to eradicate this limitation have just recently resulted in a breakthrough with this situation. A new unique method allowing the heat treatment of a filter patch has been developed via the Membrane Glass Fiber Filter. The Membrane Glass Filter can withstand temperatures up to 550°C. This allows the Analyst the same benefits as Analytical Ferrography regarding particle composition and as to whether the observed particles are of a Ferrous or Nonferrous nature. This is accomplished by placing the filter onto the hot plate for 90 seconds like the Ferrogram mentioned previously.
Images #1 and #2 show particles examined via the Filter Patch Test method using the Bichromatic microscope. This analysis was conducted on a sample extracted from the inboard bearing of a crude pump at a large refinery. The particle was identified by a trained Analyst as bearing wear. However, the composition could not be determined. This was critical as there are both steel and Babbitted bearings in this equipment.
Images #3 and #4 illustrate similar particles, however the patch had been heat treated at 360° C for 90 seconds. The mottled appearance of these particles identified them as being composed of a Babbitt material.
By determining the composition of the particles seen via the Patch Test the Analyst is now capable of further pinpointing the exact source of the damaged components within the equipment.
Conclusion: The case study of the NASA James Webb Telescope indicates that you should maintain a very clean fluid for long standing operating machinery. And combining the technology of ferrography techniques for heat treatment and the availability of glass membrane filter withstanding a temperature of 550 degrees Celsius, easily advancing the diagnostic capability of the patch membrane filter. Learning the metallurgy on the membrane filter opens up many directions to resolve and answer questions regarding the equipment being monitored.
This technique allows the analysts to narrow down her/his hypothesis and most of all, help create other opportunities to further investigate the problem. We could change the heat treatment temperature up or down in other membrane patch usage for other applications. This unexplored opportunity creates many areas to apply the technique. Having the glass membrane patch allows new discoveries to be uncovered. An amendment will be submitted to ASTM to expand the Patch Test Standard in 2023. Thanks to all the staff members involved with NASA case study and the research on the patch testing this technical paper would not be a success.
References:
Raymond J. Dalley received his mechanical degree from both Queensborough Community College and Northeastern University in 1977. He has been performing research, manufacturing, sales, and marketing with Ferrography (Wear Particle Analysis) for the past 39 years with Trico Corp. Currently an Ferrography Instrument Business Development Manager, his responsibilities include Project Manager for the Ferrographic Instrument Group. Mr. Dalley also gives lectures worldwide for the Electric Power Research Institute (EPRI), Vice-Chair for ASTM D96 Sub-Committee and has been a member for Society of Tribological Lubrication Engineers for over 38 years.
Russ Loede has been an employee of Trico Corporation for over 33 years and has been in numerous positions within the organization. Throughout those years he has continuously performed Wear Particle Analysis and Lubricant Condition Data Analysis and provided maintenance recommendations for many types of industries. Russ has also been instrumental in regard to training customers in the technique of Wear Particle Analysis. These customers include the United States Army, numerous stateside customers, and companies in both South Korea and Singapore. Russ is a United States Air Force Veteran and has obtained certificates from MIT, STLE, and other associations in the field of Tribology, Equipment, and Lubrication.
Ray Dalley has been performing research, manufacturing, sales and marketing with ferrography (wear particle analysis) for the
past 30 years.