Case Study: An Efficient Maintenance Strategy for Reciprocating Compressors
A client operates two reciprocating compressors, both of which are critical to the process. This particular plant produces a semi-finished product that is needed in another plant for the production of the end product. The reciprocating compressors are periodically inspected for rider band wear every 12 weeks, and to do so a shutdown is required. Only one compressor has a redundant machine, but with a lower production capacity. This means that production loss during the shutdown is inevitable.
The semi-finished product is stored in silos to compensate for the production loss and allow the production of the end product to continue during the shutdowns in this plant. Nonetheless, shutdowns of these reciprocating compressors could add up to tens of thousands of euros in production loss. Not to mention the mechanics needed to provide service to the compressors, which adds up to another large expense. The client recognized this inefficient method, which became particularly evident when taking into account the unnecessary shutdowns as a result of working with a fixed inspection interval. It was not irregular that the complete production was stopped only to find that the rider bands did not need a replacement, a highly inefficient and costly process.
A change of strategy
The client wanted to eliminate the need for inspection shutdowns to improve productivity, reduce operational costs, and change the maintenance operation from periodic to condition-based. They were looking for a reliable solution that would be applicable and financially accessible for both compressor setups. In collaboration with our partner CPI, Istec has provided a solution that allows the client to move from a preventive towards a predictive maintenance strategy.
RecipSys 200 monitoring solution
The RecipSys 200 is a compact monitoring system for reciprocating compressors. It delivers accurate real-time data of rider band wear, eliminating the need for periodic production shutdowns for manual inspections. Due to its low technical footprint, the RecipSys 200 is the perfect solution to tackle the clients’ challenge.
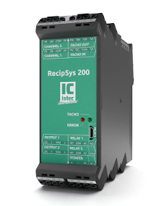
The RecipSys 200 uses two sensors; a phase trigger (reference) to filter the displacement signal to the right phase angle, and rod position sensor (proximity) to measure the rod position. The phase trigger makes the measurement much more accurate than any overall measurement.
Read the RecipSys 200 application note for more information »
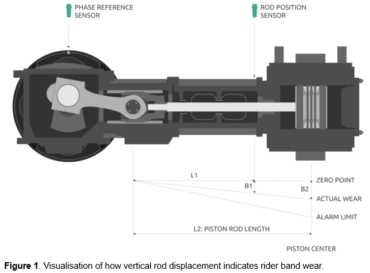
The monitoring system enables the trending of rider band wear. This data can be used to accurately estimate when maintenance is required. Subsequently, the resources and materials needed to prepare for a shutdown can be scheduled in advance.
It is important to note that the rider bands do not always wear down gradually, making an online monitoring system essential. In this case the rider bands are made of PTFE (Teflon), which could melt as a result of incorrect cooling. The material then attaches to the cylinder wall, which causes friction between the rider bands and the cylinder wall. This will excessively accelerate the process of rider band wear. The RecipSys 200 immediately detects the acceleration of the wearing process and triggers an alarm.
Compressor setups
The reciprocating compressors both had different machine specifications:
Compressor 1
Type: 1-cylinder compressor
Driver: Electromotor
Gas to compress: Recycle gas consisting mainly of hydrogen.
Running speed: 750 RPM
Rod diameter: 40 mm
Measuring position: The rod drop sensor is positioned above the piston, as the distance between the sensor and the rod increases due to rider band wear.
Phase trigger position: In axial direction, on the flywheel.
Process situation: The machine is critical to the process and there is no redundant machine. A shutdown of this machine means no production at all.
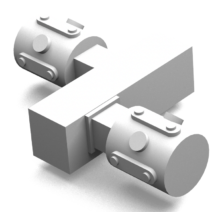
Compressor 2
Type: 4-cylinder compressor
Driver: Electromotor
Gas to compress: Hydrogen
Running speed: 500 RPM
Rod diameter: 40 mm (for all rods)
Measuring position: The rod drop sensor is positioned above the piston rod as the distance between the sensor and the rod increases due to rider band wear.
Phase trigger position: In axial direction, on the flywheel.
Process situation: The machine is critical to process, but there is a redundant machine. However, the redundant machine has a lower process capacity.
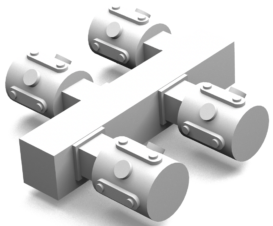
Installation and implementation
Two RecipSys 200 units were implemented in the 4-cylinder compressor and one unit in the 1-cylinder compressor. A complete turn-key solution was delivered to the client, including sensors, cables, cabinets and accessories. CPI prepared the compressors so Istec could install and adjust the sensors correctly.
Output signals
The 4-20 mA output signals go directly to the DCS for trending and analysis. The DCS has a pre-alarm which indicates emerging failures at an early stage. The relay outputs of the RecipSys 200 are used to shut down the compressors through the DCS. The trigger point of the alarm is at 0,4 mm remaining clearance between the piston and the cylinder wall. Another relay output is used to indicate the sensor status through the voltage and current of the sensor (Sensor OK) and the system temperature and general functioning (System OK).
The raw output of the RecipSys 200 can be used for analyses during commissioning. In addition, if any problems occur, this output can be used to check the system without influencing the input signal.
Result
The reciprocating compressors are now both running with online rider band monitoring, negating the need for periodic inspection shutdowns. The system monitors a key mechanical indicator and provides data that is crucial for condition-based maintenance (CBM) strategies on these compressors. The system has a low installation footprint and is friendly to use and to maintain. The client now has more control over the compressors, while being able to the cut the costs of maintenance.
Adorei conhecer seu blog, tem muito artigos bem interessantes. anydesk