At Petasense, we talk to a lot of companies that are interested in IIoT or wireless Predictive Maintenance (PdM), but aren’t sure where to start. The range of options available and perceived complexity can be daunting.
Asset reliability is a journey, and wireless technologies can enable it by providing more frequent data, data on difficult-to-reach assets and automated analysis. Whether you already have an established PdM program in place or are just getting started, we have distilled it down to a practical guidebook of the seven steps to take before going wireless.
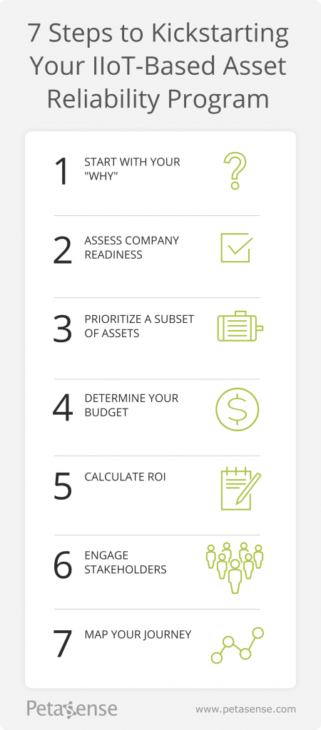
Step 1: Start with your “why”
Many companies are using condition monitoring to predict problems, but they still have failures which develop between data collection routes. Variations in operating conditions or sensor placement can make comparison over time a challenge.
Many of the companies that approach us are spurred to action after experiencing a failure which wasn’t caught with periodic condition monitoring and realizing that they need more frequent data on the condition of their assets.
This could be one very compelling reason to start thinking about wireless PdM, and there could be others such as maintenance cost reduction, mitigating potential risks, key employees retiring, or a need for increased visibility into current asset condition.
Whatever the reason, the first step of setting up an IIoT-based Asset Reliability Program is to understand what is driving the need for it so you can select a program that fits.
All projects should be driven by a clear goal.
Step 2: Assess your organizational readiness
Technology is only one piece needed to successfully implement an asset reliability program. Without the right processes and culture, technology implementation will fail.
In a reactive maintenance culture that embraces “overtime heroes,” it is going to be more challenging to implement wireless than in one that is already seeing the value of vibration, thermography, or other predictive technologies.
Take a careful look at the processes, such as how maintenance is currently being scheduled and performed. Are you in firefighting mode, where the maintenance team is trying to get the asset back up and running at all costs to equipment reliability? Do the mechanics trust recommendations coming from predictive technologies?
As a company, if you don’t have a culture or processes to support this shift, you shouldn’t buy technology with the expectation that it will fix all problems.
Step 3: Prioritize a subset of assets for a proof-of-concept
Start with an understanding of asset criticality and use that to drive your strategy for continuous monitoring. This will help prioritize assets to select for a pilot.
Usually the most critical assets such as turbines are instrumented with online protection systems, while Balance of Plant equipment such as pumps, motors and gearboxes are monitored with periodic walkaround condition monitoring or not monitored at all. Failures on these BOP assets can cause major production losses.
In order to determine the priority for continuous monitoring, start with a criticality analysis (either formal or informal). This means assigning a score for safety, production, economic, and environmental criticality — if there is a functional failure of the asset, does it impact safety, reduce production, incur high costs or have an environmental impact?
In some cases, you will determine that the asset is not critical and doesn’t need to be monitored. For those that are more critical, identify what the failure modes are, and how can you detect them. It could be via operator rounds or periodic or continuous condition monitoring. The techniques could be oil analysis, vibration, thermography, ultrasonic, motor current analysis or other.
Last step would be to identify the frequency interval of the task. This will depend on the time to failure, which is dictated by the failure mode. The assets that will benefit the most from continuous monitoring will be those with a higher criticality and a short time to failure.
This entire exercise is best done in a team, bringing together operations, maintenance and lubricators to collect the inherent knowledge in your organization, but it doesn’t have to cost hundreds of thousands of dollars.
Usually, the people closest to the equipment will immediately know which equipment has problems or is the most critical.
There could be other starting points as well. Perhaps an asset is the bottleneck in the production line, and you want to bring in real-time condition data to trend in parallel with operational data like pressure or flow. It is estimated that 85% of equipment is not instrumented, and continuous wireless monitoring can collect data and easily put it into your existing SCADA or data historian.
Step 4: Determine your budget
IIoT sounds expensive, but these projects don’t have to cost a lot. The most successful implementations start small; they focus on ~10 assets that have the greatest need, and build credibility from a pilot program.
It is important to understand the budgeting process and decision makers in your company. There is no standard decision making process across industry, so find out who needs to be involved to approve it. If your company has a corporate initiative, it may need to go through approval with IT or digital transformation teams. If it is low enough, it could be approved by the plant or engineering manager.
The cost of implementation will also depend on the vendor that you select. Even if you don’t have a vendor selected, it is good to know a rough ballpark of how much condition monitoring will cost. For a pilot project with ten assets, a reasonable budget would be between $15,000-$30,000.
When calculating your budget, take into consideration the scope of services provided by the vendors you are considering. Does it include analysis of the data, or do you have expertise in-house? If the vendor provides only software, using existing systems to conduct analytics, keep in mind that it only covers your existing sensorized assets, and if you are trying to monitor assets that don’t have sensors, you will need to add in the cost of installing sensors and wiring. Include installation and training costs as well.
Step 5: Show me the money
Maintenance departments are always being asked to cut their budget. Unless there is a major failure which makes condition monitoring top of mind, it can be difficult to free up money.
So, how can you make the case to invest money today in order to reduce money later? First, think in financial terms. How many assets are you starting with, and what is their impact on production? Whether production is measured in terms of lost revenue or contribution margin, there is a clear relationship between asset availability and production.
There are various calculators that help you create an ROI for Predictive maintenance. At the most basic level, you would want to consider:
- Current # of hours of unplanned downtime for assets being considered
- Cost per hour of lost production
- Cost per hour of lost productivity (employee cost, overtime, or contractor costs to repair)
- Cost of expedited parts
- Frequency and cost of major PMs
- Estimated cost of the system you are looking to install, including the product, training, support, and any ongoing fees
There are various other areas where you could build a calculator, such as lost orders (customer satisfaction), reducing off-spec product (quality), reducing spares held, or reducing safety incidents. Usually eliminating unplanned downtime is enough to justify the system because eliminating 1-2 events will almost always pay back the system.
Identify other sources that can help free up funding. Many companies have digital transformation or corporate reliability initiatives in place and there could be money available for proof-of-concept trials that demonstrate a positive ROI for new technologies.
Step 6: Build organizational support across departments
While the ultimate user is usually the Reliability Engineer, there are many other stakeholders that should be involved before implementing. These include IT, corporate reliability or corporate digitalization teams, process engineers, plant managers, and operations. Don’t get lost in bureaucracy, but make sure that you understand and clearly communicate the benefit to each role and engage them collaboratively.
For example, operations managers care about meeting production targets, and if you can show how this will increase uptime, you can find an ally to champion the project.
Successful implementations have a technical person who is respected within the maintenance team. The technical person could be an existing analyst, a maintenance supervisor, or a process engineer that is able to lead the program. He or she should have a view not only of the data, but of the impact and be able to articulate the benefits.
One of the current downfalls of predictive maintenance, is that it is considered a “black box” that only the analyst can access or interpret. For a continuous monitoring project, success comes by opening the visibility of the program up to more people so everyone can see how the equipment condition is operating and what risks exist. This will increase credibility of the person leading the initiative and provide visibility into the successes.
Step 7: Remember, reliability is a journey
As you get started, make sure you have a roadmap for where you are going. Think about how you would expand to different types of assets and measurement points. Consider what existing systems you have such as data historians or CMMS and map out the ideal data integrations. Don’t get lost in analysis-paralysis, but think strategically and align your vision with the vendors you are considering.
When you are selecting suppliers, evaluate cultural and technological fit, industry experience, and common vision.
The cheapest supplier is not always the best, and consider that preventing even one or two failures is more important than getting the best upfront price. Total cost of ownership is not the same as price!
If you have time, go to reliability-centered conferences such as the Reliability Conference, SMRP, IMC, Hannover Messe, or EuroMaintenance, and learn from vendors and practitioners.
When you are evaluating suppliers, do your homework and ask the right questions, such as:
- What other companies have you worked with in my industry and can I talk to them?
- What is your roadmap for long-term development?
- What support can I receive?
- What equipment can you monitor (now and future development)?
- Can you interface with my existing systems?
- How long will implementation take and who needs to be involved?
- What kind of training is required?
- What are the total costs (one time and recurring)
Over the course of your journey, you will always find ways to continuously improve your program.